It’s an interesting time in history of advanced process control (APC), a term that encompasses a range of sophisticated software tools and technologies used to optimize plant performance, primarily in the process industries. The software has been around in some form for more than 30 years, but as the people and processes in oil refining and petrochemical plants have changed, so have the software tools.
“If you go back to the very beginnings of advanced control, the people who did this employed brute force, shear determination and will to get the job done,” says Robert Golightly, APC expert for AspenTech, Burlington, Mass., the largest of the few pure software companies focused on the process industries. “They had crude tools, ugly command line interfaces. And these guys had to know everything. It was like dropping out of a helicopter in the jungle with a pocketknife.” Saravanan Prabakaran, advanced process control specialist for Yokogawa Corp. of America, Sugarland, Texas agrees.
“Earlier in the ‘80s and ‘90s, the APC tools and techniques were difficult to use and needed special hardware for implementation, which meant users ended up spending more for APC implementation. With the advancement of powerful computers, APC is today available anytime, and everywhere, with minimal cost investment and greater return on investment,” Prabakaran says.
Ten or so years ago, things improved. The tools got better, the skillsets were greater, and APC specialists had gained experience. “APC guys were married to a single plant. They were the gods of their universe. And in the last five years, we’ve cracked problems that have been around since the beginning,” Golightly says. “So today, clients who have been around APC for a while know the benefits. They’re not asked to justify the project anymore.”
Today, APC is well-established—and it’s still improving. Golightly says top-tier refining companies “have 500-600 copies of [an APC] application installed.” Prabakaran gives the following list of processes that have benefitted from Yokogawa’s offering: alkylation, ammonia, catalytic reformer, cracking furnace, delayed coker, ethylene oxide, ethylene glycol, ethyl benzene and styrene monomer, fractionator, hydrotreator, olefins, and polyethylene, among others.
Now the questions are, how do I implement additional applications faster, and how do I streamline the model maintenance burden?
Advanced definitions
To see how APC has evolved, some definitions are in order, courtesy of Rick Van Fleet, global pulping strategy marketing solution leader for Honeywell Process Solutions, Phoenix. “Regulatory control is the lowest level of controlling a process: Read a temperature, for example, send it to a PID controller, output instructions to a valve. Advanced regulatory control involves some sort of feedforward—a look up table, something based on a setting from an algorithm, but it’s still a single-input, single-output system. Advanced process control is simultaneous control of multiple inputs and multiple outputs.”
The specific technology that performs APC is what has varied over the years, and varied among vendors. “Moving up from single loop controllers, there were periods where fuzzy logic was used. This is a heuristic method, which refers to experience-based techniques for problem solving and discovery,” says Van Fleet. “There were also the use of neural networks. None of these techniques have gone away, but there’s not a great deal of academic research on those topics now. The predominant technique now is model predictive, or multivariable predictive, control (MPC).”
Some claim advanced regulatory control is a type of advanced process control that is equally useful. Regardless, “MPC has become virtually synonymous with APC,” says Dick Hill, vice president of the ARC Advisory Group, Dedham, Mass. “MPC has earned widespread respect and acceptance due to its often-spectacular payback by enabling processes to operate closer to constraints, increasing production, yields or product consistency, or some combination of the above.”
Despite the considerable implementation cost often involved, Hills says users have cited MPC projects that have delivered return on investments in 18 months or less—sometimes much less.
In a just released market study (“Real-time Process Optimization and Training Worldwide Outlook,” www.arcweb.com/res/rpo), Hill makes the distinction between APC, which includes model-based software to direct and control process operations, and online optimization, which continually monitors the state of the process and through a reference model predicts an optimum operation path.
“Online optimization goes beyond advanced control to optimize processes based on an economic objective function. Online or real-time optimization represents the pinnacle achievement in process optimization,” Hill says.
Data analytics
John Caldwell, APC product marketing manager at Emerson Process Control, Austin, Texas, says “A lot of the advanced control [software] is becoming more of a commodity technology. For example, we have the tools to test and simulate everything off-line. Most other vendors are providing the same. But we’ve integrated a lot of the system and status information into the DCS controller.”
The next challenge, says Caldwell, is how do you identify areas where problems can occur? “A new area for us is we are extending loop monitoring to statistical analytics. That’s where we look not just at instruments but also at faults in the process and the root cause of those faults, “ says Caldwell. “In our next release of Delta V, we’ll have a product for batch analytics. We also have a product in beta testing for advanced analytics.”
>> Click here to read how the pulp/paper and power gen Industries are embracing advanced control.
Data analytics gets users into the area of online optimization that Dick Hill mentioned. Terry Blevins, Emerson’s APC expert, blogs at ModelingandControl.com and has just released a new book co-authored with Willie Wojsznis and Mark Nixon entitled, “Advanced Control Foundation.” It replaces and updates their earlier book, “Advanced Control Unleashed,” with online workshops that teach the essential concepts of APC. Two chapters in the book cover data analytics.
“It’s a huge area in the business world and becoming much more important in process industries. It opens up a new world for improving operations. Fault detection can be related to economics benefits,” says Blevins.
Specialty chemicals manufacturer Lubrizol has worked with Emerson over the past five years to develop software for on-line batch analytics. This new functionality is in field trials at Lubrizol’s Rouen, France plant and is expected to be available in the next version of Delta V.
“They had done data analytics offline and after the fact,” says Blevins. “But they wanted to detect a fault before it affected quality. Batch is the hardest area. Material transfers from one process to another, and all the measurements change. But with this tool, you can have fault detection capability available online and in real time, and you can tell the operator the root measurements. What we’re doing is unique. It’s making that information available in real time so operators can make proactive changes.”
The main thing experienced APC users want is faster implementation of software, and easier ongoing maintenance of software models so they reflect the current reality of plant operations. DCS vendors address the implementation problem by integrating APC software with the DCS. They and others address the model maintenance problem with—what else?—automation.
“APC is built on an empirical model, so it’s always been true that you have to get your hands dirty in data,” says AspenTech’s Golightly. “Generally, when you go to collect this data, you have to take these controllers offline. That’s bad. Nobody’s happy. When you take the controller off-line, you’re not operating at peak efficiency.”
You also have to go back in and clean up that data—it’s iterative and recursive when you build these models—as well as clean out the bad data so you’re not teaching your model bad concepts, says Golightly. But APC software vendors have discovered ways to gather data, construct their algorithms and deliver new data back to the system so users don’t have to take controller off-line.
Boiler optimization
Invensys Operations Management (Houston, Tex.) brought its APC tool, Connoisseur, to Wisconsin Public Service, a regulated electric and gas utility in the U.S. Midwest. Invensys applied MPC to the challenges of firing optimization for one of the utility’s large (585 MW gross), relatively new, coal-fired boilers.
According to Bernie Begley, WPS controls engineer, when the new boiler was installed in 2008, WPS got the latest generation of a high efficiency supercritical boiler and turbine. It came with the full complement of emissions reduction equipment and a modern DCS with an integrated APC combustion optimization system. The advanced controls—to improve the heat rate and performance—were specified to come later.
Begley said, “After I had my year and a half on the boiler, Don came here to help us find ways to make it better.” Don Labbe is a consulting control engineer with Invensys, and a specialist in combustion optimization and power boilers. “It was a brand new unit, so there were not a lot of places to make things better. But he found a way to balance the O2 and make other changes, so that now, not only do we save money on efficiency and heat rate, we also save money on over spraying of ammonia.”
>> Click here to read about the many choices and approaches to APC software.
WPS installed Invensys Connoisseur and Labbe implemented closed-loop step testing on the MPC application. Connoisseur periodically tests the boiler’s firing and adapts the models to capture the characteristics of shifting relationships among variables in the process.
“It’s essentially an extension to the APC system to do model maintenance in an automated fashion,” says Tom Kinney, product manager for advanced applications for Invensys, “and different people call it different things: Smart testing or automated step testing. It is definitely something being exploited more and more.”
With the merger and acquisition activity of the past few years and workforce changes in the future, improvements to APC tools can’t come quick enough.
“A complex skill set is required to be good at APC, and good at the economics that are now a factor, so we’re moving to blended-skills models,” says Golightly. “Automation allows blended skills teams.” Which is good, he says, because “the people who have the battle scars are looking longingly at retirement right now. Seventy percent of the people who do this are going to be out of the workforce soon, and there’s three decades of knowledge in these people’s heads that’s going to go away.”
When it comes to APC, Golightly adds, “we think there are maybe 400 people on earth who are really good at this” and as those people move around and retire, others will take their place. With better tools, “mere mortals can now apply APC.”
Companies in this Article
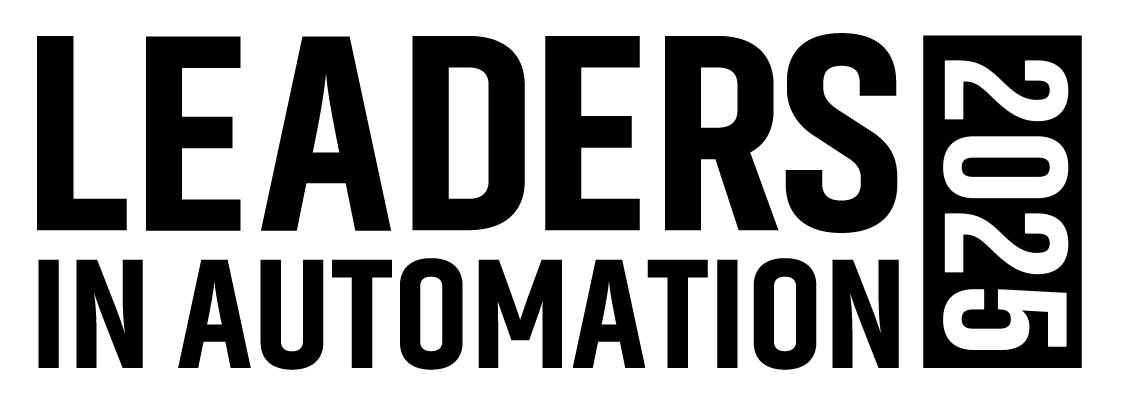
Leaders relevant to this article: